Parent page: Capturing Your Design Idea as a Schematic
Schematic Validation and Configuring the Verification Options
To validate your design, choose the Validate PCB Project <ProjectName> command from the main Project menu. To validate the project focused in the Projects panel, you can also use the
control at the top of the panel.
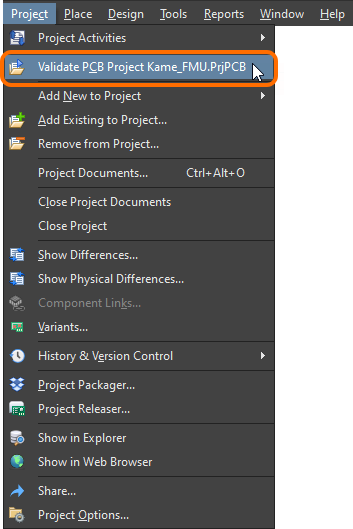
Validate your design using the Validate PCB Project <ProjectName> command.
The software checks for logical, electrical, and drafting errors between the Unified Data Model and project checking settings. If validation errors and warnings are enabled for display on the schematic (enabled on the Schematic – Compiler page of the Preferences dialog), an offending object will display a colored squiggle beneath it. Hovering over the object will display a pop-up hint that summarizes the violation. A notification is also displayed in the Messages panel.
Use the controls associated with the
Object Hints entry in the
Connectivity Insight Options region (the
System – Design Insight page of the
Preferences dialog) to determine the launch style for object hints (
Mouse Hover and/or
Alt+Double Click).
There are a large number of drafting and electrical checks that can be performed on the validated design. These are configured as part of the project options. Select the Project » Project Options command from the main menus to open the Project Options dialog. The default settings will not suit every design and, therefore, it is important to become familiar with the options and how to configure them to suit your design.
Drafting Checks
During validation, common drafting and editing errors are checked in accordance with the settings on the Error Reporting tab of the Project Options dialog. The error checks are organized in groups, for example, Violations Associated with Nets, Violations Associated with Components, etc. The groups are listed alphabetically in the dialog. The Report Mode of each violation can be changed to one of four values by clicking on it and selecting the desired value in the drop-down.

Configure the required error checks on the Error Reporting tab of the Project Options dialog. Click within the Report Mode cell of a violation to change it for this violation.
Generally, it is better to first validate the design and examine the warnings with the default settings. For those warnings that are not an issue for the current design, the reporting level can be changed.
See the PCB Design Violation Types section below for detailed information about each error check.
Connectivity Checks
The electrical connectivity is checked in accordance with the settings on the Connection Matrix tab of the Project Options dialog.
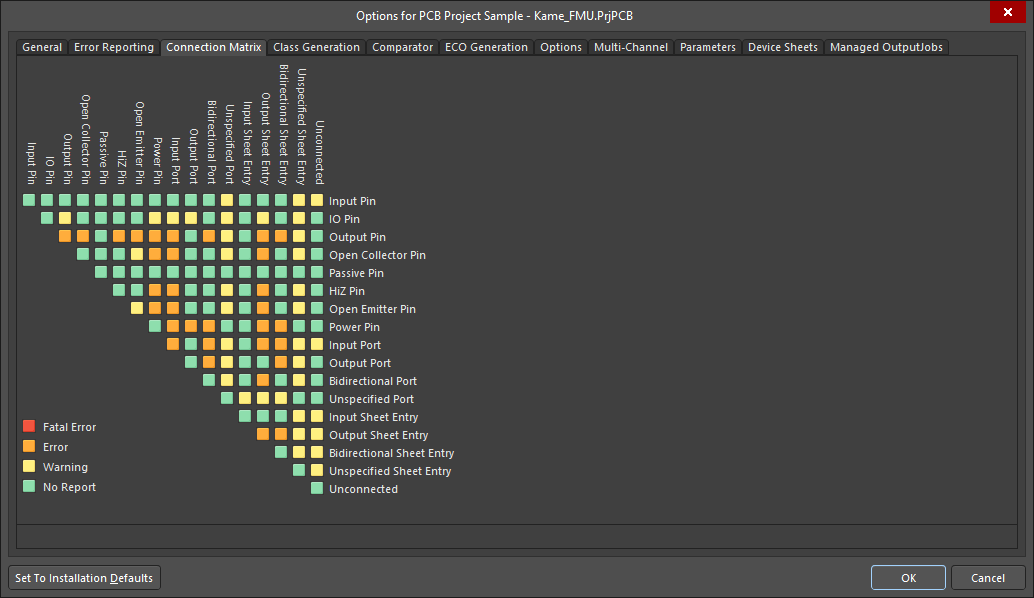
The Connection Matrix defines which electrical conditions are allowed and which are not allowed.
The matrix provides a mechanism to establish connectivity rules between component pins and net identifiers, such as Ports and Sheet Entries. It defines the logical or electrical conditions that are to be reported as warnings or errors. For example, an output pin connected to another output pin would normally be regarded as an error condition, but two connected passive pins would not.
Click on the small square in the matrix to change a particular rule. Each rule determines the reporting level for a given pin/net identifier combination. There are four possible values for each rule: Fatal Error
, Error
, Warning
, and No Report
.
The Error Reporting and Connection Matrix settings must be examined and set to suit the requirements of the current project.
Interpreting Messages and Locating Errors
When the project is validated, every condition that generates a warning or error is listed in the Messages panel. Note that the Messages panel will only open automatically if there is at least one Error
or Fatal Error
condition. To check for a Warning
, you will need to open the panel manually by clicking the Panels button on the bottom-right of the design space then choose Messages. Once the project has been validated, the panel will list any warnings and errors that have been detected.

The Messages panel displays the warnings and errors detected in the project.
The Messages panel is command central for presenting violations. Things to be aware of include:
- The Messages panel has two regions – the upper grid region summarizes the warnings/errors; the lower region gives details of the currently selected warning/error.
- Double-click on a message to cross-probe to that warning/error. Double-click on a detail to show that specific object.
- You can click on any of the Messages panel column headings (e.g., Class, Document, Message) to assist in sorting the errors and warnings.
- Right-click in the Messages panel then use the Group By sub-menu options to group the errors and warnings by a specific criteria.
-
Right-click in the Messages panel then use the appropriate Clear command to delete messages or use the Export To Report command to export the messages to a report.
Clearing messages does not necessarily mean the messages have been resolved. The same unresolved messages will be listed after performing validation again. Message clearance is a visual aid when resolving errors in the design that allows you to manually remove messages as you feel they have been resolved. Validation must be launched again to obtain an up-to-date picture of any violations that still exist.
- The panel includes warnings and errors detected from settings in both the Error Reporting tab and the Connection Matrix tab.
- When you right-click on a warning/error in the Messages panel then select the Place Specific No ERC for this violation command, you will automatically cross-probe to the error location and a No ERC directive will appear on the cursor, ready to place on the error location. Press Tab to edit the properties of the directive prior to placement, if required:
- As a generic directive, suppress all error checks at the point that the directive is placed.
- As a specific directive, only suppress the specified error checks at the point that the directive is placed.
Resolving a Warning or Error
It is important to address each warning or error that is detected. The default error settings tend to be conservative since it is better for the software to err on the side of being cautious and let you decide if the testing boundaries can be relaxed. For example, your design may require IO pins to be connected to Input ports, requiring you to adjust the appropriate cell in the Connection Matrix tab. Another common error check to be changed is the Nets with no driving source, requiring you to disable that check in the Error Reporting tab.
There will be situations when you want to test the entire design for a certain condition, but you want to ignore a warning/error at a specific point in the circuit. For example, you might want to allow a net to be renamed at a specific location, but only in that location. This can be done by placing a No ERC directive at that location.
Using the No ERC Directive
Object page: No ERC
When you need to allow a specific point in the circuit to not report an error, place a No ERC (Electrical Rules Check) directive on that point (Place » Directives » Generic No ERC) meaning do not flag a warning/error at this location. Set the No ERC symbol style and color to suit its role in the circuit in the No ERC mode of the Properties panel.

Place No ERC directives to suppress warnings or errors at a specific location.
Note that No ERC directives can be excluded from printouts, if required, by enabling the relevant option(s) in the Print dialog.

No ERC directives can be excluded from schematic printouts by configuring related options in the Print dialog.
You can place a Specific No ERC directive directly at the error location from the Messages panel (right-click then choose Place Specific No ERC for this violation as shown in the images below) or at the violation.

The right-click command makes it easy to place a specific No ERC directive directly at the error location, either from the Messages panel or at the violation.
Note that No ERC directives cannot be used to suppress all types of error checks. When the No ERC dialog is in the Violation Types mode, it displays a list of the violation types that can be suppressed. Use this as a guide to learn which error tests can be suppressed.
PCB Design Violation Types
Violations Associated with Buses
Bus indices out of rangeExpandСвернуть
This violation occurs when the index of a constituent net connected to a bus lies outside the range specified by the net to which the bus is associated.
Notification in the Messages Panel
A notification is displayed in the Messages panel in the following format:
Bus index out of range on <NetPrefix> Index = <NetIndex>
where:
NetPrefix
is the prefix of the constituent net connected to the bus (e.g., A
for net A8
, connected to a bus associated to net A[0..7]
).
NetIndex
is the erroneous index of the constituent net (e.g., net A8
has an index of 8
).
Recommendation for Resolution
Either amend the index of the offending net so that it lies within the correct range, or rename the net altogether. The latter would be typical if you have named the net by mistake and it is not a constituent of the net transported by the bus object.
Bus range syntax errorsExpandСвернуть
This violation occurs when the syntax of the net to which the bus is associated is specified incorrectly.
Notification in the Messages Panel
A notification is displayed in the Messages panel in the following format:
Bus range syntax error <NetName> at <Location>
where:
NetName
is the name of the parent net to which the offending bus object is associated.
Location
is the X, Y coordinates for the offending bus object's electrical hotspot.
Recommendation for Resolution
Correctly define bus syntax of the offending net identifier (e.g., net label, port, sheet entry, etc.). The correct syntax should appear in one of the following formats:
NetName[LowerIndex..UpperIndex]
NetName[UpperIndex..LowerIndex]
For example, consider a bus that carries two constituent nets, A0
and A1
. The bus syntax in this case should be A[0..1]
or A[1..0]
. Examples of incorrect syntax would include: A[0.1]
, A[1-0]
, A[0,1]
, A[..1]
, and A[0..]
.
Illegal bus range valuesExpandСвернуть
This violation occurs when at least one index in the syntax for a net associated with a bus is negative in value.
Notification in the Messages Panel
A notification is displayed in the Messages panel in the following format:
Illegal bus range value <BusLabel> at <Location>
where:
BusLabel
is the defined bus labeling where the illegal value has been detected.
Location
is the X, Y coordinates for the offending bus object's electrical hotspot.
Recommendation for Resolution
Correctly define bus syntax of the offending net identifier (e.g., net label, port, sheet entry, etc.). The correct syntax should appear in one of the following formats:
<NetName>[<LowerIndex>..<UpperIndex>]
<NetName>[<UpperIndex>..<LowerIndex>]
LowerIndex
and UpperIndex
can be zero or a positive integer, but cannot be negative in value.
Mismatched bus label orderingExpandСвернуть
This violation occurs when two net identifiers associated with the same bus slice define bus labels with ordering that is not in the same direction (ascending or descending).
Notification in the Messages Panel
A notification is displayed in the Messages panel in the following format:
Mismatched bus ordering on <NetName> Low value first and High value first
where:
NetName
is the name of the parent net to which the mismatched bus ordering is associated.
Recommendation for Resolution
Identify the net identifiers (port, net label, sheet entry, etc.) whose bus ordering is not consistent. Determine the correct ordering and amend the naming for the erroneous object.
Mismatched bus widthsExpandСвернуть
This violation occurs when two net identifiers associated with the same bus slice define bus labels with differing widths. For example, a port, with the name A[0..7]
, might be connected to a bus whose attached net label is defined as A[0..15]
.
Notification in the Messages Panel
A notification is displayed in the Messages panel in the following format:
Mismatched bus widths on bus section <NetName> (<BusSize1> and <BusSize2>)
where:
NetName
is the name of the parent net to which the mismatched bus objects are associated.
BusSize1
is the width of the first of the offending bus objects.
BusSize2
is the width of the second of the offending bus objects.
Recommendation for Resolution
Identify the net identifiers (port, net label, sheet entry, etc.), the bus label widths of which are not consistent. Determine the correct width and amend the naming for the erroneous object.
Mismatched Bus/Wire object on Wire/BusExpandСвернуть
This violation occurs when a wire object is incorrectly connected to a bus, or a bus object is incorrectly connected to a wire. For example, port A
might be connected to a bus, but the correct bus label syntax (e.g., A[0..1]
) has not been entered for the port's name. In effect, the port is a single signal (or wire) object that is now erroneously connected to a bus.
Notification in the Messages Panel
A notification is displayed in the Messages panel in the following format:
<ObjectIdentifier> at <Location> placed on a <ObjectType>
where:
ObjectIdentifier
represents the mismatched object, which can be either a bus or wire object (e.g., pin, port, power port, net label, off-sheet connector, sheet entry). The identifier will appear in one of the following two formats:
- For a bus –
Bus <Object> <Name>
(e.g. Bus Net Label GND_BUS[..]
).
- For a wire –
Wire <Object> <Name>
(e.g. Wire Port TXD
).
Location
is the X,Y coordinates for the object's electrical hotspot.
ObjectType
is the object on which the offending object has been placed – either a wire or a bus.
Recommendation for Resolution
To resolve the issue, consider the following:
- Is the connection correct? – should a bus connecting to the object really be a wire and vice versa?
- Is the object defined correctly? – for a bus object, ensure that the object's name is specified using the correct bus syntax in the form
<Name>[<LowIndex>..<HighIndex>]
or <Name>[<HighIndex>..<LowIndex>]
. For example, a byte-wide data output port might be specified as DAT_OUT[7..0]
. For a wire object, ensure that the object's name defines a single signal and is not defined using bus syntax.
Mixed generic and numeric bus labelingExpandСвернуть
This violation occurs when two net identifiers (port, net label, sheet entry, etc.,) connected to the same bus slice differ in their bus syntax – one defines a bus range in numeric format (e.g., A[0..2]
), while the other defines the range in a generic format (e.g., A[0..b]
).
Notification in the Messages Panel
A notification is displayed in the Messages panel in the following format:
Mismatched generic and numeric bus labeling on <NetName> <Level> value first and Generic
where:
NetName
is the name of the parent net to which the mismatched bus labeling is associated.
Level
depends on the numeric ordering for the net. If ascending (e.g., [0..2]
) Level
will appear as Low
. If descending (e.g., [2..0]
) Level
will appear as High
.
Recommendation for Resolution
Determine which of the offending objects is erroneous in its bus label specification and change it accordingly.
The use of Generics in bus names is not supported. Ensure that numeric values are used instead.
Violations Associated with Components
Component has been deletedExpandСвернуть
This violation occurs when at least one component has been deleted from a project design. Operating as a 'soft delete', deleted components are moved to a dedicated Trash location where they can be retrieved (Restore) or completely removed (Permanently Delete) from a deleted entry's menu options (⋯) in the browser interface of the connected Workspace.
Notification in the Messages Panel
Where a design project is using a component that has been deleted, this is indicated during project Validation by demonstrating the warning in the Messages panel.
A notification is displayed in the Messages panel in the following format:
ComponentName: Component has been deleted
where:
ComponentName
is the name of the Workspace component.
Recommendation for Resolution
If the component was deleted by mistake, it can be restored by someone with appropriate access rights from the Trash page of the Workspace's browser interface. Otherwise, replace the component used in the design with another equivalent component that is available in the connected Workspace.
Component Implementations with invalid pin mappingsExpandСвернуть
This violation occurs when compiling an Integrated Library Package (*.LibPkg
) and the pin mapping between the schematic component and the linked model is found to be invalid.
Notification in the Messages Panel
A notification is displayed in the Messages panel in the following format:
ComponentName: Could not find port <ModelPinNumber> on model <ModelName> for pin <ComponentPinNumber>
– PCB model related
ComponentName: Could not map port <ModelPinNumber> on model <ModelName> to a pin
– simulation model related
where:
ComponentName
is the name of the component in the source schematic library.
ModelPinNumber
is the expected designator for the pin/pad that could not be found on the linked model.
ModelName
is the name of the model that is linked to the component.
ComponentPinNumber
is the designator of the pin on the source schematic component to which the erroneous pin of the model is mapped.
Recommendation for Resolution
Resolution involves accessing the mapping between the schematic symbol and the target domain model. To do this, you'll first need to be viewing the properties for the applicable schematic library component. Double-click on the entry for the component in the Components list of the SCH Library panel to access the Properties panel, with the properties for that component loaded.
If the PCB model related violation message is displayed, select the model in the Footprint section of the panel and click the
button underneath the list to access the PCB Model dialog. Once there, click on the Pin Map button to access the Model Map dialog. In the Component Pin Designator column, find the pin number flagged by the message (ComponentPinNumber
). The violation arises because the corresponding entry in the Model Pin Designator column points to a pad designator that does not exist in the PCB model. Amend the entry as required. Typically there will be a one-to-one mapping, with the designators on both sides the same.
If the simulation model related message is displayed, select the model in the Models section of the panel and click the
button underneath the list to access the Sim Model dialog. Once there, click on the Port Map tab. This violation will arise when the model pin is not correctly mapped to a pin of the schematic component. This can happen when the entry for the model pin has been set to a pin that is already mapped, or to Not Connected
. Amend the entry as required.
Component revision has inapplicable stateExpandСвернуть
This violation occurs when at least one placed instance of a Component Item Revision – placed from a connected Workspace – is detected to be in an inapplicable state. For example, the component is currently Depracated
or Obsolete
and should therefore have no place on the latest design spin. Applicability is determined through the Allowed to be used in designs option in the State Properties dialog. From within the Edit Lifecycle Definitions dialog, access this dialog for the required state, either by double-clicking on the state's entry within the parent lifecycle definition or by selecting its entry and clicking the edit icon that appears (
). When this option is enabled, an Item Revision in this state is permitted to be used in a design. It is deemed to be Applicable. If this option is disabled, an Item Revision in this state cannot be validly used and is deemed Inapplicable (or non-applicable).
The
Edit Lifecycle Definitions dialog is itself accessed from the
Data Management – Servers page of the
Preferences dialog, by clicking the
Properties button for the Workspace to which you are actively signed in, then selecting
Lifecycles from the drop-down menu.
Notification in the Messages Panel
A notification is displayed in the Messages panel in the following format:
Component <Designator> <Comment>: Component revision has inapplicable state
where:
Designator
is the component instance's Designator.
Comment
is the component instance's Comment.
Recommendation for Resolution
Use the Item Manager dialog to choose a replacement Component Item Revision that is valid for use in the design. Do this for each component that is in an inapplicable state. Alternatively, you can switch out an existing Component Item Revision for a different revision, or revision of a different Component Item at the individual component level. Select the component on the schematic to access its properties through the Properties panel. In the Properties section of the panel, either click the Update button to use the latest revision of the current Component Item, or click the
button at the right of the Design Item ID field to access your Workspace, and browse for another Component Item Revision to use.
Use controls available through the Properties panel or Item Manager dialog to choose a later revision of the Item that is in an applicable state or, if this is not possible (the Item, in general, is not for design use), choose an applicable revision of a different Item.
Notes
- If a placed component loses connection with its source Workspace – for example, the Workspace from which it was placed is disconnected or you are signed out from your Workspace – it will violate the
Component revision has inapplicable state
check. This will be reflected in the Messages panel with an entry in the form: Component <Designator> <Comment>: Can't perform revision status validation: Failed to get session: Access denied! User login required for this service.
- You can also catch components that are being invalidly used within a design during the design release process. Add and configure Component State Checking to your overall release validation regemin.
Component revision is Out of DateExpandСвернуть
This violation occurs when a component – placed from a connected Workspace – is detected to be out of date.
Notification in the Messages Panel
A notification is displayed in the Messages panel in the following format:
Component <Designator> at <Location>: Component revision is Out of Date
where:
Designator
is the component instance's Designator.
Location
is the X, Y coordinates marking the origin of the offending component instance.
Recommendation for Resolution
Use the Item Manager dialog to identify and update components that are not the latest revision. The Item Manager includes a Revision Status column, for any components that are not at the latest revision the component's status will be Out of Date. Select the out-of-date component(s), right-click and choose Update to latest revision from the menu. Once this has been done, Generate an ECO to apply these changes to the affected schematics.
Alternatively, you can switch out an existing Component Item Revision for the latest revision, at the individual component level. Simply select the component on the schematic to access its properties through the Properties panel. In the Properties section of the panel, click the Update button to use the latest revision of the current Component Item.
Note
If a placed component loses connection with its source Workspace – for example the Workspace from which it was placed is disconnected or you are signed out from your Workspace – it will violate the Component revision is Out of Date
check. This will be reflected in the Messages panel, with an entry in the form: Component <Designator> <Comment>: Can't perform revision status validation: Failed to get session: Access denied! User login required for this service.
Components containing duplicate sub-partsExpandСвернуть
This violation occurs when the same part of a multi-part component instance has been placed more than once in a schematic design. For example, you have placed a 74HC32
component with designator U9
, but have inadvertently placed two instances of part one of this component, resulting in two instances of U9A
in the design.
Notification in the Messages Panel
A notification is displayed in the Messages panel in the following format:
Component <ComponentName> has duplicate sub-parts at <Location1> and <Location2>
where:
ComponentName
is the name of the offending component in terms of its designator and library reference.
Location1
is the X, Y coordinates for the first instance of the particular sub-part.
Location2
is the X, Y coordinates for the duplicate instance of the particular sub-part.
Recommendation for Resolution
Change the part number for the offending parts as required, using the Increment Part Number command – available from the main Edit menu or from the Part Actions sub-menu (when right-clicking over the part). The advantage of launching the command from the Edit menu is that you remain in increment mode, allowing you to cycle through the part numbers until you reach the desired one.
Components with duplicate pinsExpandСвернуть
This violation occurs when two or more pins in a component have the same designator.
Notification in the Messages Panel
A notification is displayed in the Messages panel in the following format:
Duplicate pins in component Pin <Identifier1> and Pin <Identifier2>
where:
Identifier1
is the identifier for the first instance of the duplicated pin, represented by the part designator-pin designator pairing
Identifier2
is the identifier for the second instance of the duplicated pin, represented by the part designator-pin designator pairing.
Recommendation for Resolution
Change the designator of the offending pin(s) accordingly, so that each has a unique assignment. Pin designators can be edited from within the schematic editor for a component that has already been placed:
- If the component pins are not locked, you can simply select the pin and edit its designator through the Properties panel.
- Otherwise, edit the pin(s) using the Component Pin Editor dialog. With the component selected in the design space, access to this dialog is made from the Properties panel by clicking the
button, below the Pins section, on the Pins tab of the panel.
Typically, the duplication will reside in the library component, in which case you should edit the pin designator for that component in the source schematic library and then pass the change on to placed instances of the component, using the Update From Libraries (Schematic Editor) or Update Schematics (Schematic Library Editor) commands. Both commands are available from the main Tools menus of these editors respectively.
Note
Only one violation instance will be listed in the Messages panel for each distinct component. A component may well have more than two pins with the same designator, but when investigating the violation using the Details region of the panel, only the first two duplicate pins (in alphabetical pin name order) will be listed.
Duplicate Part DesignatorsExpandСвернуть
This violation occurs when at least two parts across source schematic sheets in a design have the same designator associated with them.
Notification in the Messages Panel
A notification is displayed in the Messages panel in the following format:
Duplicate Component Designators <PartDesignator>
where:
PartDesignator
is the offending designator.
Recommendation for Resolution
Assign different and unique designators to the duplicates as required. This can be done manually by editing each offending designator or through the use of the Annotate dialog (Tools » Annotation » Annotate Schematics).
Alternatively, reset the duplicate component designators first using the Tools » Annotation » Reset Duplicate Schematic Designators command then use the Tools » Annotation » Annotate Schematics Quietly command to annotate without launching the Annotate dialog.
Generic ComponentExpandСвернуть
This violation occurs when a Generic Component has been included in a final design. Generic Components can quickly be placed in a design without the need to find and choose a specific manufacturer part from the available component sources and are intended as placeholders that are easily replaced by a suitable component.
The Generic Components functionality is not supported when connected to a NEXUS Server Workspace.
Notification in the Messages Panel
A notification is displayed in the Messages panel in the following format:
Generic Component <PartDesignator> is placed at <Location>
where:
Designator
is the placed generic component instance's Designator.
Location
is the X, Y coordinates marking the origin of the offending generic component instance.
Recommendation for Resolution
When a design has progressed to the point where a Generic Component can be replaced with a specific physical component, you may use the Replace Component dialog by selecting the ellipsis menu in the Design Item ID field of the Properties panel. Note this also can be done from the Item Manager or through the project's ActiveBOM document.
Mismatched hidden pin connectionsExpandСвернуть
This violation occurs in multi-part components when a hidden pin common to more than one sub-part is connected to different nets.
Notification in the Messages Panel
A notification is displayed in the Messages panel in the following format:
Mismatched hidden pin connections in Pin <Identifier> and Pin <Identifier>
where:
Identifier
is used to identify the pin in question. The identifier appears in the format PhysicalComponentName-PinDesignator
(e.g., U2-7
).
Recommendation for Resolution
Reassign the offending pin(s) to the correct nets. A hidden pin is assigned to a net by entering the net name into the Hidden Net Name field in the SCHLIB List panel or the SCH List panel when the panel is displaying pin properties. If this is being done in the SCH List panel, right-click in the panel and enable the Show Children option to list the pins in the panel.
Mismatched pin visibilityExpandСвернуть
This violation is related to the power pins (VCC and GND) of a multi-part component. Typically, these pins are associated with part 0, are automatically connected to the VCC and GND nets for the design, and are hidden. If for one of the component parts, you enable visibility of such a pin, it is no longer connected to the target power net and the error will be flagged.
Notification in the Messages Panel
A notification is displayed in the Messages panel in the following format:
Pin is visible in one sub-part and hidden in another sub-part
Recommendation for Resolution
Either disable the display of the offending power pin(s) in the design space or, if keeping the pins displayed, ensure that a VCC and/or GND power port object is attached to the pin(s) accordingly.
Missing Component ModelsExpandСвернуть
This violation occurs when compiling an Integrated Library Package (*.LibPkg
) and a linked model for a component in the source schematic library could not be found.
Notification in the Messages Panel
When the linked model is a footprint model or simulation model, a notification is displayed in the Messages panel in one of the following formats:
<ComponentName>: Could not find <ModelName>
– when the model search scope is Any
.
<ComponentName>: Could not find <ModelName> in <LibraryName>
– when the model search scope is Library Name
.
<ComponentName>: Could not find <ModelName> in <Path>
– when the model search scope is Library Path
.
where:
ComponentName
is the name of the component in the source schematic library.
ModelName
is the name of the footprint, or simulation model, that is linked to the source component and which could not be found.
LibraryName
is the name of the library file specified to contain the linked model.
Path
is the absolute path to a library file specified to contain the linked model.
When the linked model is a signal integrity model, the message is displayed in the Messages panel in the following format:
<ComponentName>: Could not find 'GenericEntity' in <Path>
where:
ComponentName
is the name of the component in the source schematic library.
Path
is the absolute path to a library/model.
Recommendation for Resolution
When the problem is a linked footprint or simulation model
This issue is typically caused by one of the following scenarios:
- The model name is incorrectly specified when defining the model link.
- The linked model does not reside in the specified library file.
- The library file containing the linked model has been moved or deleted.
The first port of call in resolving this violation is the associated setup dialog for the model type you are linking to – the PCB Model dialog, or the Sim Model dialog. In each case, check and ensure:
- The name of the model to which you are linking is correct, and
- The correct option is used to locate the library/model file in which that model resides.
The format of the displayed error message depends on the search scope you have enabled when locating the model, and can be of great help when tracking down the problem with the model link:
- If the model could not be found in a specified path (search scope:
Library path
), ensure that the library/model file you have specified actually exists at that location and also check the library/model file to see if the model with the specified name exists within.
- If the model could not be found in a specified library/model file (search scope:
Library name
), ensure that the library/model file has been added to the Available Libraries list (Project Libraries, Installed Libraries, Project Search Paths). Also, check to make sure the library/model file contains the model with the same name specified in the link.
- If the model could simply not be found (search scope:
Any
), ensure that a library/model file – containing a model with the same name as that specified in the link – has been added to the Available Libraries list.
When the problem is a linked signal integrity model
Typically caused when the type of signal integrity model (e.g., diode, IC) is not specified, this is resolved in the associated setup dialog for signal integrity models. The easiest way to access this is through the Properties panel when viewing the properties for the selected component. Check that you are using the correct model in the Models section on the General tab of the panel and amend if necessary. The Add and
buttons can be used to create a new model (choose Signal Integrity from the list) or modify the existing signal integrity model. This will give access to the Signal Integrity Model dialog, where the Import Ibis button allows pins models to be imported from an Ibis model file.
You can add an Ibis model directly by clicking Add » Ibis model and using the subsequent Ibis Model dialog to define the link to the model and file.
Missing pin found in component display modeExpandСвернуть
This violation occurs if a missing pin has been detected in one of the display modes for a part.
Notification in the Messages Panel
A notification is displayed in the Messages panel in the following format:
<NumberOfMissingPins> missing pins in <DisplayMode> of design item <DesignItemID>
where:
NumberOfMissingPins
is the number of missing pins found in the part.
DisplayMode
is the specific graphical representation mode for the part in which the missing pin(s) has been found. A part has a Normal mode and can have up to 255 defined Alternate modes.
DesignItemID
is the Design Item ID property of the offending part.
Recommendation for Resolution
This violation typically arises when an alternate graphical mode is defined for a component, but not all pins specified in the Normal mode have been specified for the Alternate (i.e. there must be an identical number of pins between graphical display modes).
In the source schematic library, copy the missing pins from an existing display mode into the offending display mode for the component. This can be performed directly on the schematic sheet for a part that has been placed already, but you would typically tackle the problem from within the library, then push the change across (Tools » Update Schematics).
Sheet Symbol with duplicate entriesExpandСвернуть
This violation occurs when a sheet symbol contains two sheet entries possessing the same name.
Notification in the Messages Panel
A notification is displayed in the Messages panel in the following format:
Sheet Symbol with duplicate entries Sheet Entry <Identifier> at <Location1> and <Location2>
where:
Identifier
is used to represent the offending sheet entry. The identifier appears in the format SheetSymbolName-SheetEntryName(SheetEntryIOType)
.
Location1
is the X, Y coordinates for the first violating sheet entry.
Location2
is the X, Y coordinates for the second violating sheet entry.
Recommendation for Resolution
Change the name of the offending sheet entry object as required, either by editing the name in-situ or by double-clicking on the offending sheet entry and editing its Name in the Properties section of the Properties panel – which presents all properties for the selected sheet entry.
A sheet entry name can also be edited from the
Sheet Entries section on the
General tab of the
Properties panel – when browsing the properties for the selected parent sheet symbol.
Sheet Symbols with duplicated indexesExpandСвернуть
This violation occurs in a multi-channel design when two or more sheet symbols that reference to the same child schematic sheet and include the Repeat
keyword in their Designator fields have common values of channel index ranges.
Notification in the Messages Panel
A notification is displayed in the Messages panel in the following format:
Sheet Symbols <ChannelIdentifier> have duplicated indexes: <ChannelIndexList>
where:
ChannelIdentifier
is the channel identifier used in the sheet symbols' Designator field.
ChannelIndexList
is the comma-separated list of channel indexes that are duplicated across offending sheet symbols.
Recommendation for Resolution
Change the designators of offending sheet symbol objects so their index ranges have no common values, either by editing a designator in-situ or by double-clicking on an offending sheet symbol and editing its Designator in the Properties section of the Properties panel – which presents all properties for the selected sheet symbol.
Un-Designated parts requiring annotationExpandСвернуть
This violation occurs when a component in the design is found to have a default designator (with a ? suffix), i.e. either it has yet to be annotated or the designator has been reset.
Notification in the Messages Panel
A notification is displayed in the Messages panel in the following format:
Un-Designated Part <PartDesignator>
where
PartDesignator
is the default designator for the un-designated part (e.g. U?
, D?
, C?
, etc).
Recommendation for Resolution
Assign a unique designator to the offending component as required. This can be done manually by editing the designator or through the use of the Annotate dialog (Tools » Annotation » Annotate Schematics).
Alternatively, use the Tools » Annotation » Annotate Schematics Quietly command to annotate without launching the Annotate dialog.
Note
Only one error instance will be listed in the Messages panel for each distinct designator type (U?
, D?
, C?
, etc.). Multiple errors may exist.
Unused sub-part in componentExpandСвернуть
This violation occurs when a part of a multi-part component instance has not been used within the design. For example, three out of four parts for an instance of a 74HC32
component may have been placed and wired but the fourth has not.
Notification in the Messages Panel
A notification is displayed in the Messages panel in the following format:
Component <Identifier> has unused sub-part(s) (<PartNumber>)
where
Identifier
is the parent component, represented using the format Designator Library Reference
(e.g., U11 74HC32
)
PartNumber
is an integer used to indicate which specific part is not being used (e.g., 1
represents part A
, 2
represents part B
, and so on).
Recommendation for Resolution
Place the unused part and connect its inputs to the ground. To ensure the same root designator, copy an existing part for that component's instance and, after pasting, increment its part number accordingly.
Violations Associated with Documents
Ambiguous Device Sheet Path ResolutionExpandСвернуть
This violation occurs when a target device sheet – specified in the File Name field for a Sheet Symbol – has been found in multiple declared device sheet folders.
Notification in the Messages Panel
A notification is displayed in the Messages panel in the following format:
Ambiguous Device Sheet Resolution for <DeviceSheetName>
where:
DeviceSheetName
is the current entry for the parent device sheet symbol's File Name field. Unlike the entry in the File Name field, the message includes the extension too (*.SchDoc
).
Recommendation for Resolution
Use the Details region of the Messages panel to cross-probe to the device sheet symbol in question. Double-click on the symbol to access its properties through the Properties panel. In the Source section, on the General tab of the panel, the full path to the instance of the device sheet currently being used is displayed.
Remember that the device sheet instance used will be the first detected across declared device sheet folders and that these folders – declared on the Data Management – Device Sheets page of the Preferences dialog – are searched in top-down order. If the currently used device sheet is the correct instance, you can simply ignore this violation. If not, select the folder in which the correct instance exists, and click the Move Up button until that folder is at the top of the list.
Note, however, that while this may solve the immediate issue for this particular device sheet, the ambiguity will still remain. To fully resolve this issue, identify the redundant device sheet(s), and remove it (them) from the other declared device sheet folder(s).
Circular Document DependencyExpandСвернуть
This violation occurs when compiling a project after using the Create Sheet Symbol From Sheet command from the Design main menu and a schematic document that already is a child in the project is chosen in the Choose Document to Place dialog and the schematic documents chosen have Device Sheet links between each other.
Notification in the Messages Panel
A notification is displayed in the Messages panel in the following format:
Circular dependency between document <DocumentName1> and document <DocumentName2>
where:
DocumentName1
and DocumentName2
are the names of the two documents that have Device Sheet links between each other.
Recommendation for Resolution
Review the schematic documents listed in the error message and fix the Device Sheet links between them.
Missing child sheet for sheet symbolExpandСвернуть
This violation occurs when the link between a sheet symbol and a target schematic sub-document is invalid. This can occur when:
- A sheet symbol has been placed manually but no sub-level document reference has been entered into the symbol's File Name field.
- The document reference in the symbol's File Name field has been entered incorrectly – effectively targeting a document that does not exist.
- The referenced target document has been removed from the project or deleted.
Notification in the Messages Panel
A notification is displayed in the Messages panel in the following format:
Missing child-sheet in <SymbolFileName> in Symbol <SymbolDesignator>
where:
SymbolFileName
is the current entry for the parent sheet symbol's File Name field.
SymbolDesignator
is the designator of the parent sheet symbol.
Recommendation for Resolution
Check the entry in the sheet symbol's File Name field in the Properties section on the General tab of the Properties panel (when the sheet symbol is selected in the design space). The target document itself is specified in the Source section (on that same tab of the panel), with the source set to Local for a standard sheet symbol. If the required target document already exists, ensure that the document name (including extension) is entered correctly into the field. If the target document has been removed from the project and you have access to it, add it back in to the project. If the target document does not exist, right-click on the symbol and choose the Create Sheet From Symbol command from the Sheet Symbol Actions sub-menu.
Note
This error is also generated when a Device Sheet Symbol has been placed but the target Device Sheet cannot be found. The target document itself is specified in the Source section on the General tab of the Properties panel (when the device sheet symbol is selected in the design space), with the source set to Device for a device sheet symbol.
Multiple Top-Level DocumentsExpandСвернуть
This violation occurs in hierarchical designs when two or more schematic sheets are at the top level of the structure.
Notification in the Messages Panel
A notification is displayed in the Messages panel in the following format:
Multiple top level documents: <SheetName> has been used
where:
SheetName
is the name of the schematic document currently being used as the top-level sheet.
Recommendation for Resolution
This issue typically arises due to the sheet symbol on the true top sheet not targeting the intended sub-sheet correctly. To resolve this issue, first determine which schematic sheet is the intended sub-sheet. Check to see if a sheet symbol has been placed for the intended sub-sheet on the top-level schematic:
- If a sheet symbol does not exist, create it – either by manual placement or by using the Create Sheet Symbol From Sheet command (available from the main Design menu).
- If the sheet symbol exists, ensure that it references the sub-sheet. Check the entry in the sheet symbol's File Name field in the Properties section on the General tab of the Properties panel (when the sheet symbol is selected in the design space). The target document itself is specified in the Source section (on that same tab of the panel) with the source set to Local for a standard sheet symbol.
Port not linked to parent sheet symbolExpandСвернуть
This violation occurs when a port on a child sheet is not matched with a sheet entry on the parent sheet symbol. All sheet entries in the parent sheet symbol must be synchronized (matched) to corresponding ports on the child sheet.
Notification in the Messages Panel
A notification is displayed in the Messages panel in the following format:
Port <PortName> not matched to Sheet-Entry at <Location>
where:
PortName
is the name of the port on the child sheet.
Location
is the X, Y coordinates for the port's electrical hotspot.
Recommendation for Resolution
This issue can arise for a number of reasons:
- The corresponding sheet entry for the port does not exist.
- The corresponding sheet entry for the port exists but with a different name.
- The corresponding sheet entry for the port exists but with a different I/O Type.
Use Ctrl+Double Click on the port in question to ascend to the parent sheet symbol. Right-click on the sheet symbol and choose Sheet Symbol Actions » Synchronize Sheet Entries and Ports from the menu that appears. This will open the Synchronize Ports To Sheet Entries dialog for that sheet symbol.
Use the dialog to match the port in question to the required sheet entry. If the sheet entry does not exist, you can create it directly from the dialog. If the sheet entry exists but the Name and/or I/O Type differ, you can determine, as part of the match, whether the Name and I/O Type to be used comes from the port or the sheet entry.
Notes
When the sheet entry and port exist but have different Names and/or I/O Types, there will be a corresponding error message stating that the sheet entry is not matched to a port. Synchronizing the sheet entry with the port will clear both errors.
Sheet Entry not linked to child sheetExpandСвернуть
This violation occurs when a sheet entry is not matched with a port on the child sheet referenced by the parent sheet symbol. All sheet entries in the parent sheet symbol must be synchronized (matched) to corresponding ports on the child sheet.
Notification in the Messages Panel
A notification is displayed in the Messages panel in the following format:
Sheet-Entry <SheetEntryName> not matched to Port at <Location>
where:
SheetEntryName
is the name of the sheet entry associated with the parent sheet symbol.
Location
is the X, Y coordinates for the sheet entry's electrical hotspot.
Recommendation for Resolution
This issue can arise for a number of reasons:
- The corresponding port for the sheet entry does not exist.
- The corresponding port for the sheet entry exists but with a different name.
- The corresponding port for the sheet entry exists but with a different I/O Type.
Right-click on the parent sheet symbol that is parent to the sheet entry in question then choose Sheet Symbol Actions » Synchronize Sheet Entries and Ports from the menu that appears. This will give you access to the Synchronize Ports To Sheet Entries dialog for that sheet symbol.
Use the dialog to match the sheet entry in question to the required port. If the port does not exist, you can create it directly from the dialog. Where the port exists but the Name and/or I/O Type differ, you can determine, as part of the match, whether the Name and I/O Type to be used comes from the sheet entry or the port.
Note
When the sheet entry and port exist but have different Names and/or I/O Types, there will be a corresponding error message stating that the port is not matched to a sheet entry. Synchronizing the sheet entry with the port will clear both errors.
Sheet Names ClashExpandСвернуть
This violation occurs when the project contains more than one schematic document with the same name in different folders.
Notification in the Messages Panel
A notification is displayed in the Messages panel in the following format:
Project <ProjectName> contains several documents named <SchematicDocumentName>
where:
ProjectName
is the name of the project associated with the error.
SchematicDocumentName
is the schematic document that has the same name as other schematic document(s) in the project.
Recommendation for Resolution
Save the offending schematic documents with a different name.
Violations Associated with Harnesses
Conflicting Harness DefinitionExpandСвернуть
This violation occurs when there are conflicting Harness Entries for the same Harness Type, either at a graphical or textual level (in the Harness Definition File).
Notification in the Messages Panel
A notification is displayed in the Messages panel in the following format:
Conflicting Harness Definition for <HarnessType>
where:
HarnessType
is the current conflicting Harness Type.
Recommendation for Resolution
Update the Harness Definition File to reflect the changes, or remove the offending Harness Entry, or change the Harness Type of the offending Harness Entry.
Harness Definition Files for the design can be found in the
Settings\Harness Definitions Files
folder for that project, in the
Projects panel.
Harness Connector Type Syntax ErrorExpandСвернуть
This violation occurs when either the Harness Type has invalid characters (such as [ ] { } . :
) or if the Harness Type is blank.
Notification in the Messages Panel
A notification is displayed in the Messages panel.
If the Harness Type has invalid characters, this message is displayed in the following format:
Harness Connector Type <HarnessType> should not contain these characters [] {}. :
where:
HarnessType
is the current conflicting Harness Type.
If the Harness Type is blank, this message is displayed in the following format:
Harness Connector Type cannot be Blank
Recommendation for Resolution
With the offending Harness Connector selected, specify a valid Harness Type in the Properties section of the Properties panel. Ensure the entry does not contain invalid characters.
Missing Harness Type on HarnessExpandСвернуть
This violation occurs when a Signal Harness connecting Sheet Entries or connecting a Sheet Entry to a Port is missing a Harness Type.
Notification in the Messages Panel
A notification is displayed in the Messages panel in the following format:
Missing Harness Type on Signal Harness
Recommendation for Resolution
Specify a Harness Type across the Signal Harness for at least one of the objects:
- Port – specify a Harness Type in the Properties section on the General tab of the Properties panel (which presents all properties for the selected object).
- Sheet Entry – specify a Harness Type in the Properties section of the Properties panel (which presents all properties for the selected object).
Multiple Harness Types on HarnessExpandСвернуть
This violation occurs when there are multiple Harness Types defined across a Signal Harness.
Notification in the Messages Panel
A notification is displayed in the Messages panel in the following format:
Multiple harness types on harness <HarnessType1>, <HarnessType2>
where:
HarnessType1
and HarnessType2
are the multiple Harness Types specified across the Signal Harness.
Recommendation for Resolution
Specify only one Harness Type across the Signal Harness:
- Port – specify a Harness Type in the Properties section, on the General tab of the Properties panel (which presents all properties for the selected object).
- Sheet Entry – specify a Harness Type in the Properties section of the Properties panel (which presents all properties for the selected object).
- Harness Connector – specify a Harness Type in the Properties section of the Properties panel (which presents all properties for the selected object).
- Harness Entry – specify a Harness Type in the Properties section of the Properties panel (which presents all properties for the selected object).
Unknown Harness TypeExpandСвернуть
This violation occurs when a Harness Type is found but a matching definition cannot be found in a Harness Definition file. This can happen for one of two reasons:
- A Signal Harness is connected to an object (Sheet Entry, Port, or Harness Entry) with an unknown Harness Type.
- When a Harness Entry in a Harness Definition file refers to an unknown Harness Type.
Notification in the Messages Panel
A notification is displayed in the Messages panel in the following format:
Unknown Harness Type <HarnessType>
where:
HarnessType
is the current unknown Harness Type.
Recommendation for Resolution
Ensure that Sheet Entries, Ports and Harness Entries have a known Harness Type and that Harness Definitions are accurate:
- Port – specify a Harness Type in the Properties section on the General tab of the Properties panel (which presents all properties for the selected object).
- Sheet Entry – specify a Harness Type in the Properties section of the Properties panel (which presents all properties for the selected object).
- Harness Entry – specify a Harness Type in the Properties section of the Properties panel (which presents all properties for the selected object).
Violations Associated with Nets
Adding hidden net to sheetExpandСвернуть
This violation occurs when there are two or more hidden pins within the project that have the same value entered into their Hidden Net Name property. Hidden pins are sometimes used to define the power pins in a multi-part component. Typically this warning occurs when a library component with hidden pins has been used and the designer was not aware of those hidden pins.
Notification in the Messages Panel
A notification is displayed in the Messages panel in the following format:
Adding hidden net
Recommendation for Resolution
The problem arises when the following properties for the offending pin(s) occur:
- The Hide option is enabled
- The Hidden Net Name field contains the specific power net name
If it is by design then the warning can be ignored. Alternatively, you can enable the display of the pin(s) in the design space. This option may prove to be less than desirable, especially if you have many hidden pins connected to power nets. Revealing these pins in the design space can cause clutter as each pin would need to be wired to the appropriate power port object – making the design schematic(s) less easy to read.
If you choose to display the hidden pins and those pins are assigned to Part Zero, they will appear on every part placed in the project. For multi-part component power pins that are not hidden, it can be better to create a separate part in the component just for the power pins.
The Hidden Net Name field is only accessible in the SCHLIB List panel or the SCH List panel. When working with multiple objects, it can be more efficient to edit their properties in the List panel.
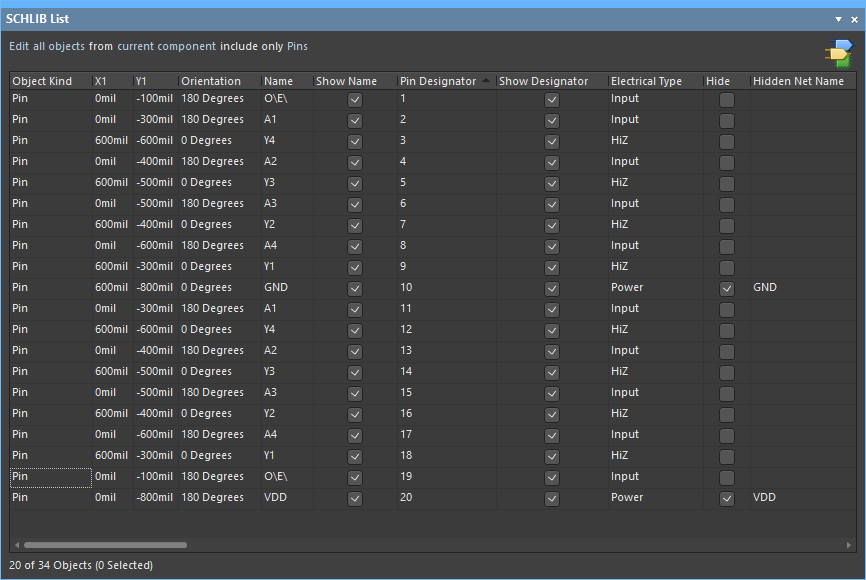
Note
Only one instance of this violation type will be listed in the Messages panel. When investigating the error using the Details region of the panel, a single entry will be listed reflecting the net that is being added. There may be multiple nets added – such as GND and VCC – but only one will be listed, determined by alphabetical order. If you clear the violation for a particular net, the next net (in order) will appear under this violation type.
Adding Items from hidden net to netExpandСвернуть
This violation is related to components and occurs when you have specified one or more pins to be hidden and connected to an existing net within the design – typically a power pin connected to VCC or GND for example.
Notification in the Messages Panel
A notification is displayed in the Messages panel in the following format:
Adding items to hidden net <NetName>
where:
NetName
is the name of the target net.
Recommendation for Resolution
The problem arises when the following property for the offending pin(s) is evident in the associated Component Pin Editor dialog:
- The Show option is disabled.
The resolution of this issue is on a per-component basis and also depends on whether a component contains multiple sub-parts.
For a non-multi-part component, enable the display of the pin(s) in the design space (enable the Show option). You will need to wire each pin to the appropriate power port for the net to which you want to connect.
The previous solution can also be applied to multi-part components, but a far better solution is to set the Part Number field to 0
. Leave the Show option for the pin disabled. Repeat for each pin that has been connected to a power net in this way. Ideally, the power net connections should be assigned through use of part 0
in the source library component.
Bus Object on a HarnessExpandСвернуть
This violation occurs when a Port, Sheet Entry, or Net Label within a Signal Harness has a name in the form [X..Y]
indicating a bus object.
Notification in the Messages Panel
A notification is displayed in the Messages panel in the following format:
Bus <Object> <ObjectName> at <Location> placed on a harness
where:
Object
is the offending port, sheet entry, or net label.
ObjectName
is the name of the offending object.
Location
is the X, Y coordinates for the offending object.
Recommendation for Resolution
Modify the name of the offending object so that it does not use bus syntax.
Differential Pair Net Connection Polarity InversedExpandСвернуть
This violation appears when the polarity of a differential pair net is not the same as that of the differential pair pin to which it is connected. For example, the positive net is connected to the negative pin, or vice versa.
Notification in the Messages Panel
A notification is displayed in the Messages panel in the following format:
Inversed connection on differential pair <PairName>: net <NetName> is connected to pin <PinDesignator> (<Polarity>)
where:
PairName
is the name of the differential pair (e.g. V_TX1
).
NetName
is the name of the offending net (e.g. V_TX1_P
).
PinDesignator
is the designator of the device pin to which the offending net is connected (e.g. E6
).
Polarity
is the polarity of the pin (e.g. negative
).
Recommendation for Resolution
Ensure that the net label attached to the connected wire is the same polarity as that of the differential pair pin to which the connection has been made. For example, if the pin name is IO_L02N_0
and the net label is V_TX1_P
, change the net label to V_TX1_N
.
If a pair of violation messages of this type appears – one for the positive net of the pair attached to the negative pin of the device and one for the negative net of the same pair attached to the positive pin – simply swap the attached net labels around.
Differential Pair Net Unconnected To Differential Pair PinExpandСвернуть
This violation appears when a differential pair net is not connected to a differential pair pin of a physical device.
Notification in the Messages Panel
A notification is displayed in the Messages panel in the following format:
Net <NetName> of differential pair <PairName> is not connected to a differential pair pin
where:
NetName
is the name of the positive or negative polarity net in the pair (e.g. V_RX1_N
or V_RX1_P
).
PairName
is the name of the differential pair (e.g. V_RX1
).
Recommendation for Resolution
A true differential pair pin is hard-wired for a physical device (e.g., a Xilinx Virtex-II Pro FPGA device). Although such a pin may appear with the identifier N
(for negative) or P
(for positive) as part of its name, you cannot make a pin differential simply by changing its name.
Consider the following when resolving a violation of this type:
- If the differential pair net is correct but has been attached/wired to the wrong pin of the device, determine the correct pin and move the net label accordingly.
- If the differential pair nethas been erroneously specified as a differential pair net, change the associated net label to the correct (non-differential) naming and remove the attached differential pair directive from the connecting wire.
- If the pin to which the differential pair net is currently connected is, in fact, not to be used at all in the design, ensure that net label, wire, and differential pair directive are removed and place a No ERC marker on it.
Differential Pair Unproperly Connected to DeviceExpandСвернуть
This violation appears when a differential pair net is not properly connected to a differential pair pin of a physical device.
Notification in the Messages Panel
A notification is displayed in the Messages panel in the following format:
Misconnected differential pair <PairName>: net <NetName> should be connected to pin <PinDesignator>
where:
PairName
is the name of the differential pair (e.g., V_TX1
).
NetName
is the name of the positive or negative polarity net in the pair (e.g., V_TX1_N
or V_TX1_P
).
PinDesignator
is the designator of the device pin to which the offending net should be connecting (e.g., E6
).
Recommendation for Resolution
This type of violation typically arises when the wire object for the differential pair net is not making an electrical connection with the target pin of the device. Ensure proper connection between the wire of the net and the device pin itself.
Duplicate NetsExpandСвернуть
This violation occurs when two nets with the same name have been detected within the design.
Notification in the Messages Panel
A notification is displayed in the Messages panel in the following format:
Duplicate Net Names <Object> <NetName>
where:
Object
is either Wire
or Bus Slice
or Element[n]
(for a bus element).
NetName
is the name of the affected net.
Recommendation for Resolution
When the design data model is being created, nets are created in the following way:
- Within each sheet, a unique net is created for each set of connected electrical objects.
- The Net Identifier Scope is then checked to determine if the design is flat or hierarchical.
- If the design is flat, the sheet-level nets are connected directly between the various sheets.
- If the design is hierarchical:
- using the Port attached to the lower-level net, the connectivity is created from that Port up to the Sheet Entry in the Sheet Symbol on the parent sheet, then
- the connectivity is created between the Sheet Entry and other connected electrical objects on the parent sheet.
To learn more about flat and hierarchical designs, refer to the Creating Circuit Connectivity in Your Schematics page.
This violation can arise when, for example:
- The design is flat and ports have been used within the design. The Net Identifier Scope is automatically (or manually) set to
Flat (Only ports global)
. The violation will occur if the same net label has been used between sheets. This is because net labels defined on each sheet, even with the same name, remain local to those sheets. The resolution, in this case, is to ensure unique net labeling is used between sheets.
- The net continuity between flattened schematic sheets is broken by the inadvertent use of ports or off sheet connectors with different names. Trace the net back to the incoming/outgoing port on each sheet and ensure the names for the ports are made the same.
- You may have the same net used in two different branches of a hierarchical design – i.e. different sheet symbols are used to reference different child sheets, but the same name is used for the top-level sheet entries and descendent ports, and the two symbols are connected by a physical wire or bus. The net continuity between these branches can be broken by the inadvertent use of sheet entries with different names or the omission of a physical bus/wire connecting the sheet entries. Ensure that the physical wire connecting the two sheet symbols is in place and wired correctly and that the sheet entries are named the same.
External and Schematic Net Names are UnsynchronizedExpandСвернуть
This violation occurs when a Net Name of a pin of a schematic FPGA component does not match the external source file Net Name of a pin.
Notification in the Messages Panel
A notification is displayed in the Messages panel in the following format:
External <NetLabelName> and Schematic <NetLabelName> are Unsynchronized for Pin <xx>
where:
NetLabelName
is the name of the offending net label.
xx
is the pin number.
Recommendation for Resolution
In the Pin Mapper dialog with the offending Pin selected, in the Schematic region, access the drop-down solution options then choose Update Pin File (
) to transfer the net name from the schematic to the external FPGA pin file then validate the project again.
Floating net labelsExpandСвернуть
This violation occurs when a net label has been detected to be floating, i.e. not attached to a wire or bus object, within the design. The message will also appear for a bus power port object that is not electrically connected to the rest of the circuit.
Notification in the Messages Panel
A notification is displayed in the Messages panel in the following format:
Floating Net Label <NetLabelName>
where:
NetLabelName
is the name of the offending net label.
Recommendation for Resolution
Ensure that the offending net label object is connected to the required wire or bus object. If the net label is redundant, delete it from the design.
Check also that the wire/bus object and associated net label are on the grid. An object can be moved back onto the grid manually or by using the Edit » Align » Align To Grid command.
Also, check that a wire is really a wire and not a line object!
Floating power objectsExpandСвернуть
This violation occurs when a power port object has been detected to be floating – not electrically connected to a component – within the design. For example, the power port may have been placed but is not yet wired up to the rest of the circuit.
Notification in the Messages Panel
A notification is displayed in the Messages panel in the following format:
Floating Power Object <NetName>
where:
NetName
is the name of the net associated with the floating power port object.
Recommendation for Resolution
Ensure that the offending power port object is connected to the circuit as required. If the power port is redundant, delete it from the design.
Note
This message is related to the standard, single-signal power port objects.
Global Power-Object scope changesExpandСвернуть
This violation occurs when a port-based object (port, off sheet connector) has been connected to a power port object. The power object can no longer exist on a global level – connected to a global power net – and is instead changed to be a local-level power net.
Notification in the Messages Panel
A notification is displayed in the Messages panel in the following format:
Global Power-Object <NetName> at <Location1> has been reduced to local level by presence of port at <Location2>
where:
NetName
is the net to which the power port object is associated.
Location1
is the X, Y coordinates for the power port object's electrical hotspot.
Location2
is the X, Y coordinates for the port object's electrical hotspot.
Recommendation for Resolution
This violation can typically arise when a power port object is incorrectly wired to a port rather than the intended pin or sheet entry. There may, however, be cases where you want to force (and use) a scope change of this kind. Assess whether the connection between the port and power port is intended and, if not, remove the power port and wire the remaining port object to its intended destination as required.
Harness Object on a BusExpandСвернуть
This violation occurs when an object such as a Port, Sheet Entry, or Harness Entry has an associated Harness Type, which represents a connection to a Signal Harness, but it is wired to a bus.
Notification in the Messages Panel
A notification is displayed in the Messages panel in the following format:
Harness <Object> <ObjectName> at <Location> placed on bus
where:
Object
is the offending Port, Sheet Entry, or Harness Entry.
ObjectName
is the label of the offending object.
Location
is the X, Y coordinates for the offending object.
Recommendation for Resolution
Ensure that the offending object (Port, Sheet Entry, or Harness Entry) is not connected to a bus, but rather a signal harness.
Harness Object on a WireExpandСвернуть
This violation occurs when an object such as a Port, Sheet Entry, or Harness Entry has an associated Harness Type, which represents a connection to a Signal Harness, however, the object is connected to a wire.
Notification in the Messages Panel
A notification is displayed in the Messages panel in the following format:
Harness <Object> <ObjectName> at <Location> placed on wire
where:
Object
is the offending Port, Sheet Entry, or Harness Entry.
ObjectName
is the label of the offending object.
Location
is the X, Y coordinates for the offending object.
Recommendation for Resolution
Ensure that the offending object (Port, Sheet Entry, or Harness Entry) is not connected to a wire, but rather a signal harness.
Missing Negative Net in Differential PairExpandСвернуть
This violation appears when a negative polarity net has not been detected for a particular differential pair object within a design. The positive polarity net for the pair does exist.
Notification in the Messages Panel
A notification is displayed in the Messages panel in the following format:
Missing Negative Net for differential pair <PairName>, positive net <NetName>
where:
PairName
is the name of the differential pair for which a positive polarity net has already been defined (e.g., V_RX1
).
NetName
is the name of the positive polarity net (e.g., V_RX1_P
).
Recommendation for Resolution
This violation typically arises in the following situations:
- A differential pair directive has not been attached to the negative polarity wire of the signal pairing. The required net label (e.g.,
V_RX1_N
) has been attached to the wire as required.
- An appropriately-named net label (e.g.,
V_RX1_N
) has not been attached to the negative polarity wire of the signal pairing. The required differential pair directive has been attached to the wire as required.
To resolve this violation, locate the negative wire object for the pair and ensure that both the net label and differential pair directive are attached and that the name of the net label is specified as required. The net label for the negative wire will be essentially the same as that for the positive wire, but with an _N
suffix instead of an _P
. Alternatively, if the negative wire object is connected to an appropriately-named port object, the Allow Ports to Name Nets option can be enabled on the Options tab of the Project Options dialog instead of attaching a net label to the wire.
Missing Positive Net in Differential PairExpandСвернуть
This violation appears when a positive polarity net has not been detected for a particular differential pair object within a design. The negative polarity net for the pair does exist.
Notification in the Messages Panel
A notification is displayed in the Messages panel in the following format:
Missing Positive Net for differential pair <PairName>, negative net <NetName>
where:
PairName
is the name of the differential pair for which a positive polarity net has already been defined (e.g., V_RX1
).
NetName
is the name of the negative polarity net (e.g., V_RX1_N
).
Recommendation for Resolution
This violation typically arises in the following situations:
- A differential pair directive has not been attached to the positive polarity wire of the signal pairing. The required net label (e.g.,
V_RX1_P
) has been attached to the wire as required.
- An appropriately-named net label (e.g.,
V_RX1_P
) has not been attached to the positive polarity wire of the signal pairing. The required differential pair directive has been attached to the wire as required.
To resolve this violation, locate the positive wire object for the pair and ensure that both the net label and differential pair directive are attached and that the name of the net label is specified as required. The net label for the positive wire will be essentially the same as that for the negative wire, but with a _P
suffix instead of a _N
. Alternatively, if the positive wire object is connected to an appropriately-named port object, the Allow Ports to Name Nets option can be enabled on the Options tab of the Project Options dialog instead of attaching a net label to the wire.
Net Parameters with no nameExpandСвернуть
This violation occurs when a parameter set object is attached to a net object (wire or bus) and at least one of the defined parameters in the set has no name assigned to it.
Notification in the Messages Panel
A notification is displayed in the Messages panel in the following format:
Invalid net-parameter name at <Location>
where:
Location
is the X, Y coordinates for the hotspot of the parameter set object associated with the net.
Recommendation for Resolution
Access the Parameter Set mode of the Properties panel for the offending parameter set object and ensure that all parameters defined within have a name assigned to them. If the offending constituent parameter is not required, simply remove it from the set.
Net Parameters with no valueExpandСвернуть
This violation occurs when a parameter set object is attached to a net object (wire or bus) and at least one of the defined classes in the set has no value assigned to it.
Notification in the Messages Panel
A notification is displayed in the Messages panel in the following format:
Invalid net-parameter value at <Location>
where:
Location
is the X, Y coordinates for the hotspot of the parameter set object associated with the net.
Recommendation for Resolution
Select the offending parameter set object in the design space to access its properties in the Properties panel. Ensure that all parameters defined in the Classes section of the panel have a value assigned to them. If the offending class parameter is not required, remove it from the set.
If the class parameter is visible in the design space, you can enter a value for it directly (click once to select, then click again to enter in-place editing), or select it and access the
Properties panel. Then enter a value for it using the
Value field in the
Properties section of the panel.
Nets containing floating input pinsExpandСвернуть
This violation occurs when an input pin for a placed part within the design has been detected to be floating, i.e. not electrically connected to any other part of the circuit.
Notification in the Messages Panel
A notification is displayed in the Messages panel in the following format:
Net <NetName> contains floating input pins (<PinList>)
where:
NetName
is the name of the offending net.
PinList
is the comma-separated list of pins in that net that are floating.
Recommendation for Resolution
This violation can arise in a number of situations. Consider the following when resolving a violation of this type:
- If the pin is not to be used within the design, either tie it to the appropriate power line (e.g.,
GND
), or place a No ERC directive on it.
- Ensure that the wiring to the pin is making electrical contact, i.e. the wire or bus connects to the pin's electrical hot spot.
- Use the Navigator panel to trace the connectivity of the parent net to which the offending pin is associated. Sometimes, a pin can be caused to 'float' when there is a break somewhere else in the net. For example, a pin might receive its signal from an input port on the sheet, which in turn is fed a signal from a linked sheet entry higher up in the design hierarchy. The input to this sheet entry may be disconnected. Fixing the connection to the sheet entry will resolve the floating input pin violation.
- Look for additional violation messages in the Messages panel that relate to the same parent net, especially those that mention unconnected objects. This can give an indication of where the break in connectivity lies.
Nets containing multiple similar objectsExpandСвернуть
This violation occurs when two or more objects of the same type (pin, port, sheet entry) and same electrical I/O specification have been detected to be connected to each other in the same parent net. For example, an Input Port
connected to an Input Port
.
Notification in the Messages Panel
A notification is displayed in the Messages panel in the following format:
Net <NetName> contains multiple <ObjectType> (<ObjectList>)
where:
- NetName is the name of the offending net.
- ObjectType is the type of object which has multiple instances found in the offending net. The entry will also reflect the object's electrical type.
- ObjectList is a comma-separated list of all instances of the object found in the offending net.
Recommendation for Resolution
Determine if the offending connected objects pose a real connectivity problem and, if so, change the I/O specification for one or both objects accordingly. If an object is redundant, remove it from the design. If an object was intended to be wired into a different part of the design and has been connected to the wrong destination (therefore, becoming part of the wrong net), ensure that it is disconnected from its current net and wired up to the correct one.
Notes
- The actual report mode used for a violation of this type is dependent on the specific object types, their electrical I/O types, and the corresponding reporting level defined on the Connection Matrix tab of the Options for Project dialog (Project » Project Options).
- The Report Mode setting on the Error Reporting tab of the Options for Project dialog has no affect on the Report Mode setting that appears for a violation of this type in the Messages panel. It is, however, used by the Online (real-time) error reporting directly within the design space. Controls for the Online reporting are available on the Schematic – Compiler page of the Preferences dialog. Note that the Online error reporting for a specific object type-I/O type pairing will not be present if the individual check for that combination in the Connection Matrix has been set to
No Report
.
Nets with multiple namesExpandСвернуть
This violation occurs when a net in the design has been detected to have multiple names associated with it.
Notification in the Messages Panel
A notification is displayed in the Messages panel in the following format:
Nets <Identifier> has multiple names (<NameList>)
where:
Identifier
represents the type of connection and the name of the net. The connection can be one of the following:
- Wire – where the identifier will appear in the format
Wire NetName
(e.g., Wire DTSA
).
- Bus – where the identifier will appear in the format
Bus Slice NetName
(e.g., Bus Slice A[0..7]
).
- Bus Element – where the identifier will appear in the format
Element[n]: NetPrefix
(e.g., Element[0]: A
).
NameList
is a comma-separated list of all names found associated with the offending net. These names can come from attached net labels, sheet entries, power ports, and off sheet connectors.
Recommendation for Resolution
This violation can be resolved by ensuring that the names of all net identifiers associated with a particular net are the same. However, in many cases, it is beneficial to use different names for a particular net – for example, when that net is present on different branches of a hierarchical design and different names better reflect the conducted signal in those branches. Similarly, you may want to describe the sheet entry of a particular sheet symbol using a different name to that of the net label attached to the incoming/outgoing wire or bus.
To freely use multiple names with nets in your design and prevent related violation messages appearing in the Messages panel, set the Report Mode for this violation type to No Report
on the Error Reporting tab of the Options for Project dialog (Project » Project Options).
Nets with no driving sourceExpandСвернуть
This violation occurs when a net in the design has been detected to have no driving source. That is, the net does not include at least one pin with one of the following electrical types:
- IO
- Output
- Open Collector
- HiZ
- Open Emitter
- Power
It is not uncommon for a net to not include a pin of one of these types, for example, it can happen when:
- A net connects from a connector pin to an input pin.
- A net connects from a series passive component (which have passive pins) to an input pin.
Notification in the Messages Panel
A notification is displayed in the Messages panel in the following format:
Net <NetName> has no driving source (<PinList>)
where:
NetName
is the name of the offending net.
PinList
is the comma-separated list of pins in that net.
Recommendation for Resolution
Edit the connector/passive component pin so that it is one of the electrical types listed above.
Nets with only one pinExpandСвернуть
This violation occurs when a net in the design has been detected to contain only one component pin.
Notification in the Messages Panel
A notification is displayed in the Messages panel in the following format:
Net <NetName> has only one pin (Pin <PinName>)
where:
NetName
is the name of the parent net.
PinName
is the component designator-pin designator identifier.
Recommendation for Resolution
By default, this message will not appear in the Messages panel. If you have enabled reporting for this violation type and want to resolve the issue, ensure that the offending net is wired to at least two component pins in the design.
Nets with possible connection problemsExpandСвернуть
This violation occurs when two objects connected to each other on the same net have mismatched electrical types that could lead to problematic connectivity. The pair of object types considered by this error check can be any combination of pins, ports, or sheet entries. For example, an Output Port
connected to a Bidirectional Port
.
Notification in the Messages Panel
A notification is displayed in the Messages panel in the following format:
<NetName> contains <ObjectType1> and <ObjectType2> objects (<Reference>)
where:
- NetName is the name of the parent net containing the possible conflicting objects.
- ObjectType1 is the first offending object type.
- ObjectType2 is the second offending object type.
- Reference is the identifier for one or both objects (e.g.,
Port PortName
, Pin PinName
, and Sheet EntrySheetSymbolName-SheetEntryName
).
Recommendation for Resolution
Determine if the offending connected objects pose a real connectivity problem and, if so, change the I/O specification for one or both objects accordingly.
Notes
- The actual report mode used for a violation of this type is dependent on the specific object types, their electrical I/O types, and the corresponding reporting level defined on the Connection Matrix tab of the Options for Project dialog (Project » Project Options).
- The Report Mode setting on the Error Reporting tab of the Options for Project dialog has no affect on the Report Mode setting that appears for a violation of this type in the Messages panel. It is, however, used by the Online (real-time) error reporting, directly within the design space. Controls for the Online reporting are available on the Schematic – Compiler page of the Preferences dialog. Note that the Online error reporting for a specific object type-I/O type pairing will not be present if the individual check for that combination in the Connection Matrix has been set to
No Report
.
Same Net used in Multiple Differential PairsExpandСвернуть
This violation occurs when the same polarity net (positive or negative) has been detected in multiple differential pair objects within the design.
Notification in the Messages Panel
A notification is displayed in the Messages panel in the following format:
Net <NetName> is used in more than one differential pair objects: <ObjectList>
where:
NetName
is the name of the positive or negative polarity net being used in multiple differential pair objects (e.g., V_RX1_N
or V_RX1_P
).
ObjectList
is a list of the differential pair objects in which the offending net is used. As the differential pair name is taken as the root of the net name, the names in this list will be identical (e.g., V_RX1 V_RX1
).
Recommendation for Resolution
This violation typically arises when the same net label has been attached to multiple wire objects upon which differential pair directives have also been attached. Locate the offending net label objects and amend the names as required.
The positive and negative wires in a pairing should have associated net labels with the same root name for the net, along with a _P
and _N
suffix respectively. For example, if two wires in a particular pair have the same net label, V_RX1_N
, change the positive wire's net label to V_RX1_P
.
Sheets containing duplicate portsExpandСвернуть
This violation occurs when two ports with the same name are detected on the same schematic sheet in the design.
Notification in the Messages Panel
A notification is displayed in the Messages panel in the following format:
Sheet contains duplicate ports Port <Identifier> at <Location1> and <Location2>
where:
Identifier
is the name of the offending port.
Location1
is the X, Y coordinates for the first instance of the particular port.
Location2
is the X, Y coordinates for the second instance of the port.
Recommendation for Resolution
Determine which of duplicate port objects is in error and either rename it or delete it from the design.
Unconnected objects in netExpandСвернуть
This violation occurs when a pin, port, or sheet entry object is not wired up to the rest of the circuit.
Notification in the Messages Panel
A notification is displayed in the Messages panel in the following format:
Unconnected <Object> at <Location>
where:
Object
is the type and name of the offending object (pin, port, or sheet entry).
Location
is the X, Y coordinates of the object on the source schematic sheet.
Recommendation for Resolution
Consider the following in order to resolve this error:
- If the pin/port/sheet entry is to be used, ensure that it is wired up to the rest of the circuit accordingly.
- If a port or sheet entry is redundant, remove it from the design.
- Tie any unused input pins to the appropriate power line.
- Place No ERC directives on unused input or output pins.
Notes
- When the unconnected object is an input pin, an additional violation message will appear alerting you to the fact that the net to which the pin is associated contains floating input pins. The identifier for the pin will be listed in that message.
- The actual report mode used for a violation of this type is dependent on the specific object type, its electrical I/O type, and the corresponding reporting level defined on the Connection Matrix tab of the Options for Project dialog (Project » Project Options).
- The Report Mode setting on the Error Reporting tab of the Options for Project dialog has no effect on the Report Mode setting that appears for a violation of this type in the Messages panel. It is, however, used by the Online (real-time) error reporting, directly within the design space. Controls for the Online reporting are available on the Schematic – Compiler page of the Preferences dialog.
Unconnected wiresExpandСвернуть
This violation occurs when a wire object is detected to be floating, i.e. not electrically connected to any part of the circuit design.
Notification in the Messages Panel
A notification is displayed in the Messages panel in the following format:
Unconnected line <Location1> To <Location2>
where:
Location1
is the X, Y coordinates for the start point of the floating wire.
Location2
is the X, Y coordinates for the endpoint of the floating wire.
Recommendation for Resolution
Ensure that the offending wire object is connected to the circuit as required. If the wire is redundant, delete it from the design. If the wire (or any other object) is off the sheet and cannot be directly selected, use the Edit » Select » Outside Area command to select it, then delete it.
Violations Associated with Others
Duplicated project filesExpandСвернуть
This violation occurs when there is more than one project file (.PrjPCB
) found in the folder of a Workspace project.
Notification
A notification is displayed in the Messages panel in the following format:
Duplicate .PrjPcb files found in this project, which can cause design files to display incorrectly in a web browser. To fix this, please remove any extra .PrjPcb files from your project folder.
Recommendation for Resolution
Remove any extra .PrjPcb
files from the project folder so it contains only one .PrjPcb
file.
Fail to add alternate itemExpandСвернуть
This violation occurs when an Alternate Part – chosen to be used for a component in a defined Variant of the active design project – cannot be added. This happens when a part with the same name, but resides in different libraries, is used across different Variants for the project. The .PrjPcbVariants
file, which stores the information for the alternate parts chosen, cannot store multiple parts with the same name, and so references to the other instance(s), resident in different libraries, will not be added. For example, consider the situation where the following variants of a design project have been defined with an Alternate Part chosen for a placed capacitor:
- Variant 1 – Alternate Part
Cap
chosen, that resides in library Lib1.SchLib
.
- Variant 2 – Alternate Part
Cap
chosen, that resides in library Lib2.SchLib
.
Floating Directive ObjectExpandСвернуть
This violation occurs when there is a floating Parameter Set directive, NoERC directive, Differential Pair directive, or Probe object.
Notification
A notification is displayed in the Messages panel in the following format:
Floating <Parameter Set directive, NoERC directive, Differential Pair directive, or Probe object> at <Location>
,
where:
Parameter Set directive, NoERC directive, Differential Pair directive, or Probe object
is the floating object located in the design space.
Location
is the X, Y coordinates for the floating object.
Recommendation for Resolution
Attach the floating Parameter Set directive, NoERC directive, Differential Pair directive, or Probe object to their intended location.
Incorrect link in project variantExpandСвернуть
This violation occurs when a single-part component has been chosen as an Alternate Part for a multi-part component – in a defined Variant for the active design project – and there is more than one part of the original base design component placed within the design. For example, consider a base design with multi-part component R1 – an isolated resistor network with 8 sub-parts. Also consider that four of those parts have been placed (R1A, R1B, R1C, R1D). Now, consider a defined variant of that base design, where an alternate part has been chosen to be used in place of that original base part. The chosen part should also be a multi-part component that can easily accommodate switching out the four sub-parts currently used in the design. However, if by mistake, a single-part resistor component is chosen as the alternate, it does not have the capacity to facilitate the switching-out of existing sub-parts R1B, R1C, and R1D. The Compiler, therefore, flags this as an incorrect link.
Notification
A notification is displayed in the Messages panel in the following format:
Incorrect link between project variant "<VariantName>" and schematic component Component <ComponentPhysicalDesignator> (<ComponentLogicalDesignator>) <BasePartComment>
where:
VariantName
is the name of the design variant in which the erroneous alternate component has been defined.
ComponentPhysicalDesignator
is the physical designator for the affected component (the designator as displayed on the compiled tab view of the relevant schematic document on which the component in question resides).
ComponentLogicalDesignator
is the logical designator for the affected component (the designator as displayed on the Editor tab view of the relevant schematic document on which the component in question resides). If the logical and physical designators are identical, this entry will not be displayed.
BasePartComment
is the value for the Comment parameter for the affected component as defined in the base design.
Recommendation for Resolution
If only one part of the original multi-part component in question is being used, then you can simply delete any other placed instances and validate the project again. Since the alternate part is a single-part component, it is sufficient for replacement for the single used part of the original multi-part component.
However, this approach, while effective, is not entirely desirable. It is more like a band-aid rather than resolving the underlying issue. A far better approach is to choose a better alternate part for the component in the relevant design variant. To do this:
- Make the relevant variant the current variant from the
Variants
folder for the parent project in the Projects panel. Switch to the Compiled tab for the document, right-click on a part of the base multi-part component, then choose Part Actions » Variants. This opens the Variant Management dialog with only the offending component in only that chosen variant presented.
- Use the Component Variation field to open the Edit Component Variation dialog.
- With the Alternate Part option still selected, use the other options in the dialog to browse to and choose a more suitable replacement component to be used in that specific variant of the design.
- Click OK to close the dialogs and validate the design project again. The incorrect link violation should have been resolved and no longer appear (unless, of course, there are multiple components with this issue, in which case repeat the previous steps).
Object not completely within sheet boundariesExpandСвернуть
This violation occurs when a design object resides beyond the extents of the schematic sheet.
Notification
A notification is displayed in the Messages panel in the following format:
Off sheet <ObjectIdentifier> at <Location>
where:
ObjectIdentifier
identifies the specific object that currently does not reside completely within the boundary defined by the sheet. The identifier is composed of the object's type and its name/designator (e.g., Port <PortName>
).
Location
is the X, Y coordinates for the object's electrical hotspot.
Recommendation for Resolution
When placing or pasting objects onto a sheet, you are prevented from placing/pasting beyond the extents of the sheet's border. This issue typically arises when the size and orientation of the sheet are changed after object placement. Consider the following to resolve the problem:
- Change the sheet orientation.
- Choose a larger sheet size.
- Move the offending objects back within the sheet boundary.
The first two options are carried out from the Page Options section on the General tab of the Properties panel (accessed when no objects are currently selected in the design space). Changing sheet size is the simplest way to resolve the issue. Moving objects manually may require layout changes to the circuit to provide enough space to accommodate the offending objects.
Off-grid objectExpandСвернуть
This violation occurs when an object is not aligned to the current Snap grid.
Notification
A notification is displayed in the Messages panel in the following format:
Off grid <ObjectIdentifier> at <Location>
where:
ObjectIdentifier
identifies the specific object that is currently off-grid. The identifier is composed of the object's type and its name/designator (e.g., Pin <PinDesignator>
).
Location
is the X, Y coordinates for the object's electrical hotspot.
Recommendation for Resolution
Ensure that the Snap grid is defined as required and enabled in the General section on the General tab of the Properties panel (accessed when no objects are currently selected in the design space). The offending object can be moved back onto the grid manually or by using the Align To Grid command.
Unsupported multi-channel alternate itemExpandСвернуть
This violation occurs when, for a given variant of a multi-channel design, different Alternate Parts have been used for a component across channels.
Alternate parts within a specific channel in a multi-channel project are supported when the Schematic.SupportForAlternatePartsInMultichannels
option is enabled in the Advanced Settings dialog. When this option is enabled, the Unsupported multi-channel alternate item
check will not be available in the dialog.
The Advanced Settings dialog is accessed by clicking the Advanced button on the System – General page of the Preferences dialog. If any changes are made in the Advanced Settings dialog, the software must be restarted in order for the changes to take effect.
Notification
A notification is displayed in the Messages panel in the following format:
There are alternate items for multi-channel item "Component <ComponentLogicalDesignator> <ComponentName>" in variant "<VariantName>". Please, check your variant configuration. Alternate parts aren't fully supported in multi-channel designs and can lead to inconsistent data
where:
ComponentLogicalDesignator
is the logical designator for the affected component (the designator as displayed on the Editor tab view of the relevant schematic document on which the component in question resides).
ComponentName
is the name of the component in violation.
VariantName
is the name of the design variant for which Alternate Part choices have been chosen across channels for the component in violation.
Recommendation for Resolution
To resolve this type of violation, either choose the same Alternate Part of the component in question for all affected channels or set the component to Fitted
or Not Fitted
for a channel so that there are no longer different Alternate Parts in use. To do so:
- Make the relevant variant the current variant from the
Variants
folder for the parent project in the Projects panel. From the Editor tab for the document, right-click on the part in violation and choose Part Actions » Variants. This opens the Variant Management dialog with only the offending component presented (across all channels).
- For each offending channel, use the Component Variation field to access the Edit Component Variation dialog.
- With the Alternate Part option still selected, use the other options in the dialog to browse to and choose the same (required) part already used in another channel. Alternatively, choose to make the component
Fitted
or Not Fitted
for that particular channel.
- OK out of the dialogs and validate the design project again. The violation should now have been resolved and no longer appear (unless there are multiple components with this issue, in which case, repeat the previous steps).
Violations Associated with Parameters
Same parameter containing different typesExpandСвернуть
This violation occurs when two parameters possessing the same name have been assigned to the same design object, but the parameters have differing types.
Notification
A notification is displayed in the Messages panel in the following format:
Same parameter contains different types <Object> <Types>
where:
Object
is the particular object to which the offending parameter is associated.
Types
shows the different types for the parameter as a pairing (e.g., BOOLEAN
and STRING
).
Since there are two offending parameters, a pair of errors will be displayed in the Messages panel. They will differ in the order of the types, with the type for the parameter in error being listed first followed by the type of the other offending parameter in the pairing.
Recommendation for Resolution
Typically, you would not have multiple parameters of the same name associated with an object. Review the parameters assigned to the object and remove the erroneous/redundant one.
Same parameter containing different valuesExpandСвернуть
This violation occurs when two parameters have been assigned to the same design object, they have the same name and are of the same type but having differing values.
Notification
A notification is displayed in the Messages panel in the following format:
Same parameter contains different values <Object> <Values>
where:
Object
is the particular object to which the offending parameter is associated.
Values
show the different values for the parameter as a pairing.
Since there are two offending parameters, a pair of errors will be displayed in the Messages panel. They will differ in the order of the values, with the value for the parameter in error being listed first followed by the value of the other offending parameter in the pairing.
Recommendation for Resolution
Typically, you would not have multiple parameters of the same name associated with an object. Review the parameters assigned to the object and remove the erroneous/redundant one.